Visite | Mavic : en quête de renouveau
Par Léo Kervran -
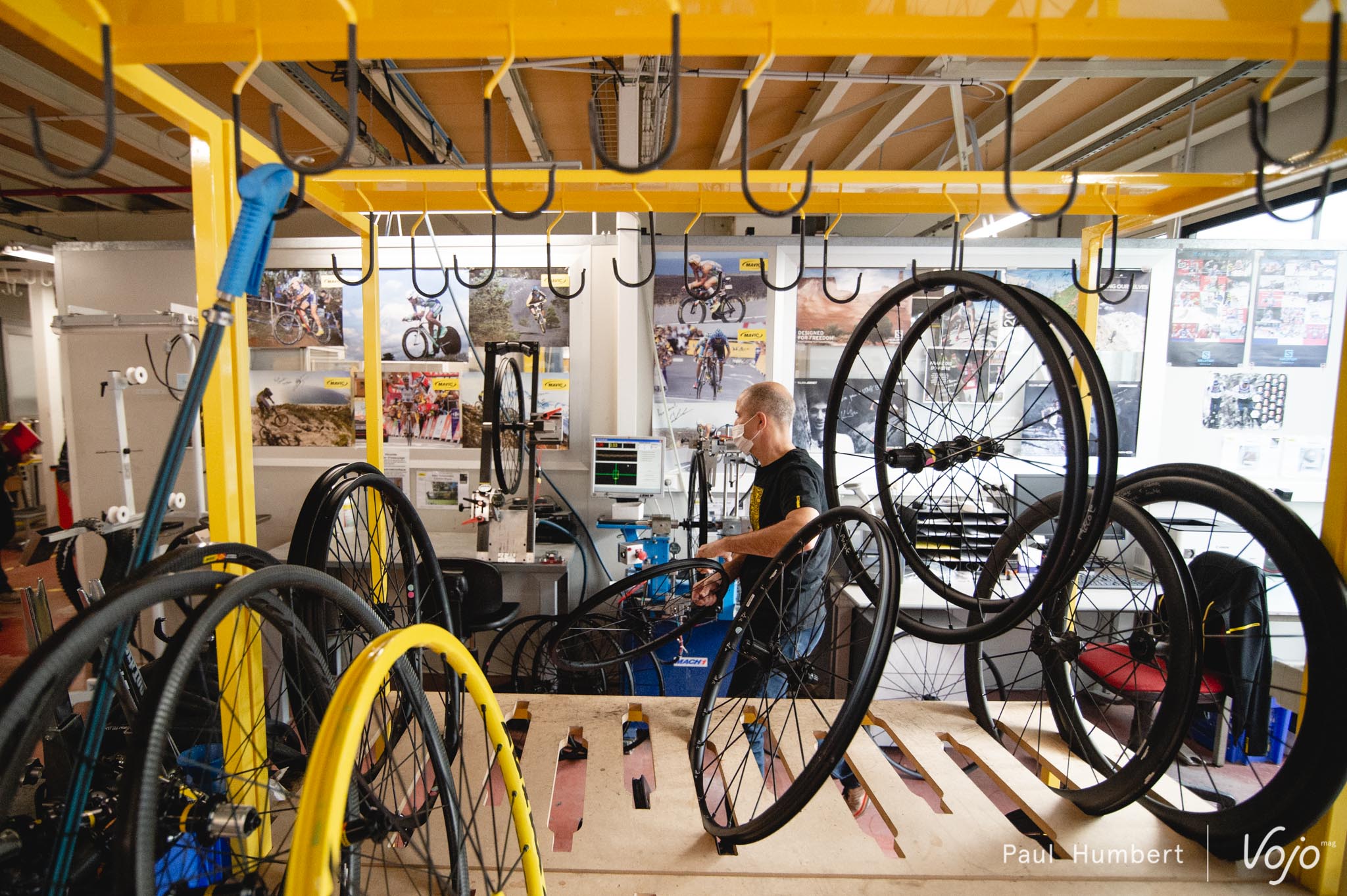
Chez Vojo, ça faisait un moment que nous voulions aller visiter Mavic. Forcément, quand le siège de la marque se situe à quelques kilomètres de l’antenne française de la rédaction, cela donne des idées. L’occasion s’est finalement présentée il y a quelques semaines, alors que la petite unité de production qu’abrite le site reprenait du service. De quoi en profiter pour faire une visite un peu plus interactive qu’à l’accoutumée…
Faut-il encore présenter Mavic ? Née en 1882, la marque est l’un des fleurons de l’industrie française du cycle et a participé aux plus grandes heures de notre sport, dans toutes les disciplines. Après quelques années compliquées qui l’ont menée jusqu’à un redressement judiciaire, elle veut aujourd’hui renaître de ses cendres et retrouver sa place parmi les grands du marché.
Même si toutes ses idées n’ont pas toujours été couronnées de succès, Mavic a en effet une longue réputation d’innovation derrière elle : jante anodisée et à crochets en 1975, roue paraculaire Comète en 1985 (plus de 10 ans après les premiers prototypes) devenue lenticulaire par la suite, transmission électrique en 1992 puis sans fil en 1999, système roue-pneu en 2010… Son implication dans le VTT remonte à plus de 30 ans puisque c’est en 1985 que la marque a sorti ses premières jantes spécialement dédiées à ce qui n’était encore qu’une pratique naissante.
Dans le milieu, Mavic s’est notamment fait connaître avec le concept Fore, lancé en 1999 et qui permet de ne percer que la première paroi de la jante pour fixer le rayon, laissant ainsi la paroi supérieure intacte et continue. Cette innovation donnera naissance la même année au système UST Tubeless, qui a permis de démocratiser le montage sans chambre à air. Quelques années plus tard, les Crossmax SLR en XC et les Deemax en DH, toutes deux très facilement identifiables (avec l’usinage ISM pour les premières et la fameuse couleur jaune pour les secondes), porteront la marque jusqu’au sommet des podiums mondiaux et feront rêver des milliers d’amateurs partout dans le monde.
La fin des années 2010 sera en revanche moins riante pour Mavic. Sur le plan technique, la marque doit faire face à des problèmes de fiabilité et une communication qui ne répond pas forcément aux attentes de ses clients, tandis qu’en arrière-plan, elle se débat avec des difficultés financières et un imbroglio autour de son propriétaire. Ce n’est que fin juillet 2020 que Mavic commence à entrevoir le bout du tunnel, avec une reprise par le groupe Bourrelier (voir notre news) à l’issue de trois mois en redressement judiciaire.
Aujourd’hui, Mavic compte 109 employés, soit un peu moins de la moitié de l’effectif présent avant la reprise par le groupe Bourrelier. Une coupe importante mais jugée nécessaire pour permettre à la marque de se redresser et de reconquérir le cœur des pratiquants.« On a retrouvé un fonctionnement de PME », nous explique Michel Lethenet, le responsable des relations presse et notre guide pour la journée. Plus de souplesse et de transparence, voilà effectivement qui ne peut pas faire de mal quand on veut concilier avant-garde technologique, performance et fiabilité pour tous les pratiquants.
Michel nous rassure également sur la place de ce que la marque appelle le soft, c’est-à-dire les casques, chaussures et vêtements. « Oubliée » lors de l’annonce de la reprise par Bourrelier, la division a toujours de l’avenir chez la marque et on ne verra pas ces produits disparaître de sitôt. En revanche, on peut s’attendre à voir des changements dans la gamme car, comme pour les roues, Mavic a entrepris de « rationaliser » son offre d’équipements. Notons aussi que la marque envisage de rapatrier la fabrication de ces produits dans l’Union Européenne (certains sont encore faits au Maghreb), comme c’est déjà le cas pour les roues.
Pour mieux comprendre son savoir-faire, Mavic nous propose de fabriquer nous-même une roue en carbone…
On le comprend, Mavic est en pleine transformation et pas mal de changements sont encore attendus dans les mois à venir, en interne comme dans les stratégies liées aux produits. En attendant, s’il y a bien une chose qu’on ne peut pas retirer à Mavic, c’est son savoir-faire. Et pour le comprendre, quoi de mieux que nous permettre de fabriquer notre propre roue en carbone ?
Le carbone, du rouleau à la jante
L’essentiel des roues a beau être fabriqué ailleurs (en Roumanie pour celles en carbone, à Saint-Triviers-sur-Moignans pour celles en aluminium), le siège d’Annecy a conservé une petite unité de production qui sert pour les prototypes et les éditions limitées, mais aussi les roues des athlètes sponsorisés par la marque et deux modèles très haut de gamme de route, les Cosmic Ultimate T et Cosmic Ultimate T Disc.
Nous changeons donc de bâtiment pour rejoindre l’atelier carbone, une grande pièce organisée autour des gigantesques tables qui permettent la découpe ou le positionnement des feuilles de carbone. Nous y retrouvons Claude Righini, chef de produit roues composites, qui va nous guider dans la fabrication de la jante.
En nous attendant, il a déjà préparé les différentes pièces de carbone (une centaine par roue) qui permettront de construire la jante. En effet, Mavic reçoit le précieux matériau sous la forme de grands rouleaux de pré-imprégné, c’est-à-dire des fibres de carbone déjà enduites de résine. Ces rouleaux, il faut ensuite les découper selon des formes bien précises pour créer les différentes pièces qui donneront naissance à la jante.
Une fois ces pièces prêtes, on passe à la première étape de la construction : la création à plat de la structure de la jante, ce qu’on voit en tant que pratiquant depuis l’extérieur. Sur les nouvelles roues Mavic, les pièces ont la forme de trapèzes pour faire apparaître une jolie alternance dans l’orientation des fibres sur le produit fini. Leur positionnement est relativement simple mais pour le faire vite et bien, c’est une autre histoire : on décolle le matériau protecteur sur une face, on place la pièce en butée dans le gabarit, on l’aplatit bien et on enlève le deuxième matériau protecteur. Ensuite, on prend une autre pièce et on recommence l’opération, en prenant soin de la poser en sens inverse pour créer l’alternance.
Ces pièces sont en fibres unidirectionnelles, une forme du carbone qui dispose de meilleures propriétés mécaniques que du carbone tissé et permet du coup d’utiliser moins de matériau pour le même résultat, donc de gagner du poids.
L’inconvénient, c’est que les fibres unidirectionnelles peuvent se délaminer plus facilement, notamment au niveau des perçages pour la valve et les rayons. Mavic utilisait auparavant un renfort tissé tout autour de la jante, mais sur les nouvelles roues, c’est différent. Chaque paroi intègre un renfort en fibre de verre et sur celle où reposent les écrous de rayons, de petits empiècements en carbone tissé sont placés au niveau de chaque perçage. L’intérêt de ce procédé, c’est qu’il permet de gagner du poids : environ 70 g par jante, simplement en supprimant l’excédent de renforts.
D’ailleurs, pas de photos pour le placement de ces renforts. Mavic a développé sa technique et ses propres outils pour les mettre en place et n’a pas envie d’être copié… De même pour l’opération qui permet de lier la structure que nous venons de fabriquer et la partie « haute » de la jante, c’est-à-dire le fond où prend appui la valve et un morceau des flancs côté intérieur.
Une fois que tout ce petit monde est relié et a pris la forme d’une roue grâce au moule, direction le four. Cette fois-ci les photos sont autorisées, mais pas de trop près car la marque garde le secret sur le processus précis de cuisson. Tout ce que l’on sait, c’est que cela passe par plusieurs phases à différentes températures et que c’est plutôt rapide : nous avons à peine eu le temps de faire un tour de cette partie bien plus active du bâtiment que notre jante était prête. La cuisson du carbone, c’est comme celle du pain du boulanger : ce n’est pas évident, cela fait appel à l’expérience, cela passe par des essais/erreurs et surtout, chacun garde sa recette jalousement.
Dernières touches
Dernière étape de fabrication que nous verrons aujourd’hui, la finition. Pas de vernis, de peinture ou quoi que ce soit sur ces jantes, le carbone est laissé tel qu’il est, mais il faut nettoyer l’excédent de résine et surtout retirer la vessie. Cette dernière, qui prend place à l’intérieur de la jante et permet de plaquer le carbone contre les parois du moule pendant la cuisson, est extraite par le trou de valve. Une autre petite source de gain de poids, comparé à une jante plus simple où la vessie resterait en place. En revanche, ça ne change rien sur le côté pratique : entre les pressions importantes pendant la cuisson et le vide réalisé pour la retirer, une vessie est soumise à de très fortes contraintes et Mavic ne peut pas prendre le risque d’avoir une quelconque fuite. Chaque vessie est donc à usage unique.
Le nettoyage de la jante ne prend que quelques dizaines de secondes sur notre roue de VTT car l’opération est simple, mais sur d’autres produits plus complexes, cela peut demander beaucoup plus de temps. Pour les Cosmic Ultimate T entièrement en carbone (moyeu, rayons et jante) que nous évoquions plus haut par exemple, chaque roue nécessite entre 2 et 8 h de travail manuel.
Ensuite, c’est perçage des trous de rayons, pose des stickers puis assemblage, pour obtenir une Crossmax SL Ultimate complète. Si Mavic donne l’impression d’être un « géant » de la roue, beaucoup d’opérations restent encore manuelles et la marque n’est pas si éloignée des artisans à certains égards. Ainsi, la tension des rayons est vérifiée et ajustée à la main sur chaque roue produite, qu’elle soit en aluminium et assemblée à Saint-Triviers ou en carbone et montée en Roumanie.
Un bref détour par l’atelier d’usinage nous permet de comprendre rapidement les différentes étapes de fabrication d’un moyeu, à partir d’un lopin d’aluminium de quelques centaines de grammes.
Après cela, la roue est enfin prête… mais pas forcément à être mise sur le marché. Si c’est un prototype ou tout simplement un échantillon d’un lot de production, elle peut aussi prendre la direction du laboratoire qualité pour y passer toute une batterie de tests.
Entre-temps, Michel Lethenet nous confie que Mavic a beaucoup mis l’accent sur ce domaine depuis environ 1 an et demi pour relever la tête, en admettant qu’il y a peut-être eu des erreurs ou des excès de confiance par le passé. Aujourd’hui, c’est pas moins de 50 mesures qui sont réalisées sur chaque modèle de roue qui rentre dans ce laboratoire.
Tests en série
Comme nous l’explique Jean-Luc Veux, responsable évaluation/qualité et maître des lieux, 5 de ces mesures sont pour la validation des normes (principalement de l’endurance) et tout le reste, c’est de l’évaluation supplémentaire mise en place par Mavic : mesures statiques, tests d’endurance, tests de choc… Cela va jusqu’à l’examen au microscope électronique des corps de roue libre pour étudier l’usure des dents !
Au passage, on en profite pour poser LA question de celles et ceux qui ont déjà eu un jour toutes les peines du mondes à monter un pneu neuf sur une roue : est-ce que Mavic réalise ce genre de test avec les différentes marques de pneu du marché ? Bonne nouvelle, la réponse est oui, mais on nous précise aussi qu’ils ont déjà remarqué que certaines marques étaient plus difficiles à monter que d’autres, avec des tolérances plutôt vers le bas de la fourchette qui laissent peu de marge de manœuvre aux fabricants de roues.
On s’en doute, reproduire en laboratoire les contraintes du terrain n’est jamais une chose aisée et il faut toute l’expérience de la marque pour concevoir des tests les plus représentatifs possible. D’ailleurs, certaines machines de la salle dédiées aux tests d’endurance sont uniques et sont protégées des attentions encore plus jalousement qu’un prototype de roue. Le laboratoire seul ne saurait cependant suffire à tester correctement un nouveau produit et comme chaque marque, Mavic dispose de toute une équipe pour mettre à l’épreuve ses roues sur le terrain.
Cette équipe, ce sont les ambassadeurs de la marques, les pilotes des teams sponsorisés par la marque (KMC-Orbea en XC, par exemple) mais aussi les ingénieurs eux-mêmes, puisqu’une bonne partie du personnel de Mavic roule. La journée se terminera d’ailleurs par une sortie sur les hauteurs d’Annecy en compagnie de Michel Lethenet et Esteban Deronzier, le chef produit VTT. De quoi oublier un moment le professionnel et les contraintes de chacun pour partager simplement un bon moment autour de ce qui nous anime tous en premier, la passion du VTT…
Fabriquer une jante en carbone soi-même, c’est quelque chose qui n’arrive pas tous les jours. Cependant, ce qu’on retient au-delà de l’expérience inédite, c’est la découverte de personnes réellement passionnées par leur métier et par l’innovation. Si on passe outre les installations dignes d’une grosse entreprise, notamment dans le laboratoire de tests, on aurait presque l’impression d’être chez une jeune PME qui aime plus que tout inventer de nouvelles choses et qui n’aurait pas pris conscience de son succès.
Cela a pu créer un certain décalage avec le marché et les attentes des consommateurs, mais à l’issue de cette visite, on se dit que c’était surtout à cause d’une trop grande envie de bien faire et d’apporter des solutions. Quitte à faire fi des « standards » et autres techniques plus ou moins universellement adoptées. Forcément, cela ne passe pas toujours, et encore moins en France où une certaine composante émotionnelle et « patriote » rentre en compte. Aujourd’hui, Mavic est en pleine reconstruction et on espère qu’elle saura tirer les leçons de ces quelques années difficiles pour redevenir une marque de premier plan, capable de jongler intelligemment entre innovation, performance, accessibilité et proximité avec les pratiquants.