Visite | Cyclik : un avenir plus vert pour nos vélos ?
Par Léo Kervran -
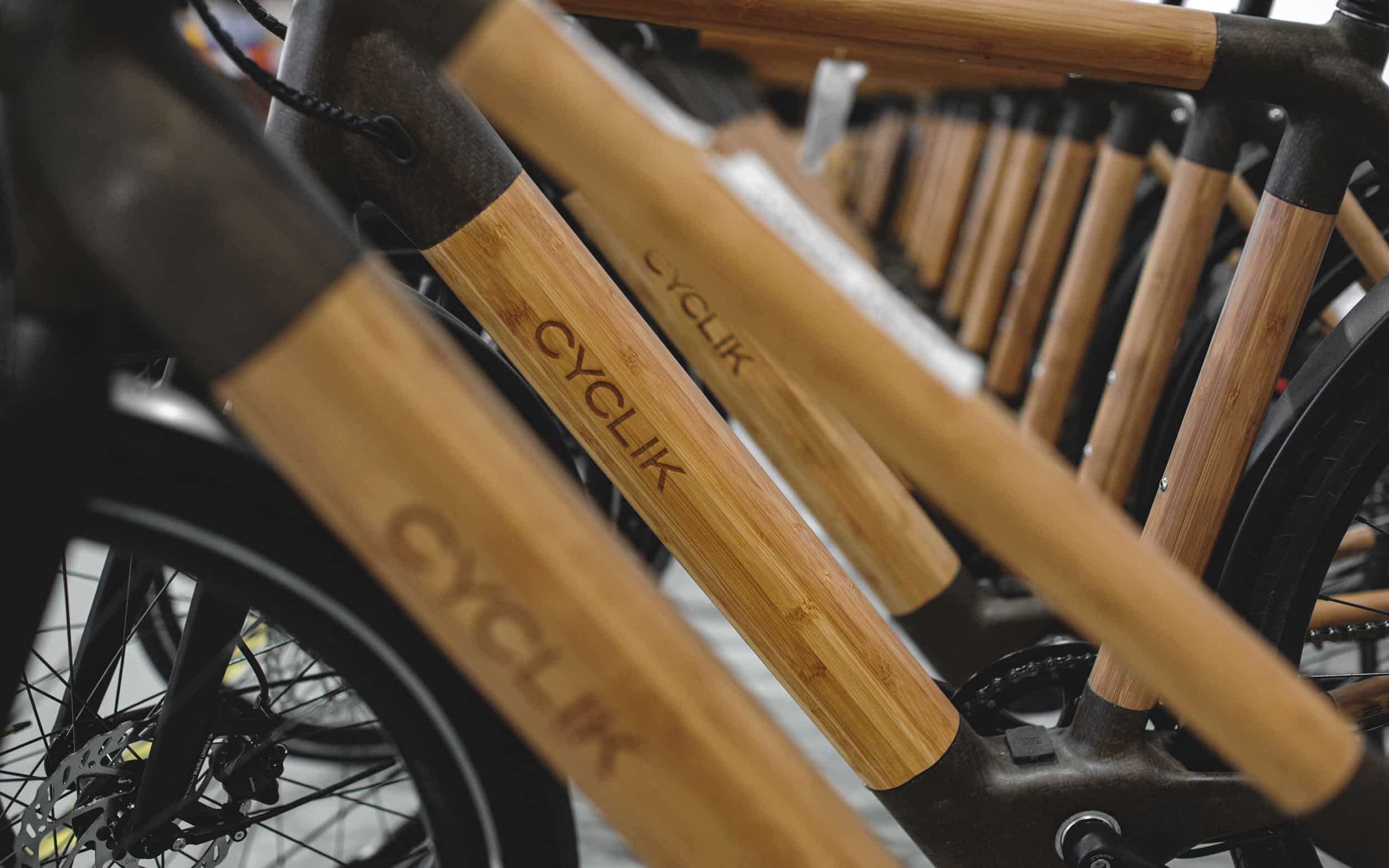
Des artisans qui fabriquent des vélos en bambou, on en connaît quelques-uns et on est même déjà monté sur des VTT dans ce matériau. Néanmoins, c’est souvent cher et cela reste un produit de niche… mais pour combien de temps encore ? Jeune marque française, Cyclik s’est lancé un défi ambitieux : industrialiser le processus et montrer que les matériaux naturels, comme le bambou ou la fibre de lin, peuvent être de vraies alternatives aux métaux et composites fossiles qui règnent en maîtres sur nos cadres de vélo aujourd’hui. Visite :
Avant l’industrialisation, il y a eu l’artisanat. Les premiers chapitres de l’histoire de Cyclik sont semblables à ceux d’autres artisans : après une pratique assidue du cyclisme sur route jusqu’à un bon niveau amateur (DN2), Félix Hébert raccroche les épingles avec des douleurs lancinantes dans les cervicales et les avant-bras. Il faut dire qu’il y a 10-15 ans, le confort des vélos n’était pas le même qu’aujourd’hui, encore moins en vélo de route…
Néanmoins, la passion du vélo et des choses qui vont vite est toujours là et Félix se prend à rêver d’un vélo qui aurait le dynamisme des machines en carbone de l’époque et le confort en plus. Titane ? Ses propriétés sont connues mais c’est cher et pas évident à travailler. Dans ses recherches, arrive alors le bambou. Le bambou ? Si on le connaît pour sa croissance très rapide et sa place de choix dans l’alimentation des pandas géants, le bambou possède aussi des caractéristiques mécaniques intéressantes qui sont étudiées et exploitées depuis longtemps dans d’autres domaines. Il n’est peut-être pas meilleur que le carbone mais pour Félix, c’est en partie compensé par l’avantage d’être un matériau naturel, qui peut s’utiliser avec très peu de transformations.
C’est dit, ce sera du bambou ! En 2014, Félix construit donc son tout premier cadre en bambou, à partir de tubes séchés choisis soigneusement et de jonctions en fibre de lins. Tant qu’à faire dans le naturel, autant rester cohérent jusqu’au bout. Au départ, l’idée n’était pas d’en faire une activité commerciale mais le résultat intrigue. D’abord les proches, puis des curieux ou curieuses de plus en plus éloignés, tentés par les promesses de ce matériau.
Premières aventures
Le mot se passe, les demandes augmentent et de fil en aiguille, Félix s’associe à un ami pour lancer Cyclik en 2017. Uniquement sur la route pour commencer, avec une cible bien identifiée : les cyclosportifs et cyclosportives, celles et ceux qui, sans accrocher un dossard tous les week-ends, trouvent tout de même une partie de leur plaisir dans l’effort. Une cible qui cherche des vélos capables d’offrir un savant équilibre entre confort (pour ne pas trop souffrir sur la durée) et sportivité (pour les sensations).
Le savoir-faire établi, les modèles se diversifient : peu à peu, Cyclik se met à fabriquer des VTT puis des vélo de voyage et même des gravel, le matériau étant particulièrement indiqué pour cette pratique « hybride » traversée aussi par un certain courant de « retour à la nature ».
Au stade artisanal, la conception d’un cadre en bambou est assez simple : il faut gérer le collage et les jonctions en fibre de lin bien sûr, mais une grande partie des qualités dynamiques du vélo repose sur le choix des tubes de bambou. En effet, ces derniers ne reçoivent que peu ou pas de modifications et à ce stade, le travail de Félix consiste beaucoup à choisir judicieusement chaque tube en fonction de leur longueur, de leur régularité ou de leur section.
L’étape capitale, c’est le séchage. Une fois bien sec, le bambou deviendra une matière inerte qui ne rencontrera pas plus de problèmes de durée de vie qu’un tube en acier. Ceci, toutefois, se passe en dehors des ateliers de Cyclik : la marque se fournit auprès de la Bambouseraie en Cévennes, à côté d’Anduze dans le Gard, un des principaux acteurs du domaine réputé pour la qualité et la régularité de ses bambous.
Bonus, c’est fait en France ! Toutefois, pour Félix, le « made in France » est une question de facilité avant même de parler de beaux principes. Avoir ses fournisseurs ou ses partenaires pas très loin, cela permet de leur rendre visite de temps à autre pour mieux définir les besoins, pour s’assurer que la production correspond à ce que l’on souhaite…
C’est la même chose pour les fibres de lin utilisées dans les jonctions entre les tubes de bambou. La matière première, qui est ensuite traitée dans les ateliers de Cyclik, vient de Normandie. En effet, la France est de loin le premier producteur mondial de lin et la région compte à elle seule pour près d’un tiers du total mondial annuel. Pourquoi aller voir ailleurs ?
Pour se rapprocher encore plus ? Félix et Cyclik y réfléchissent car la Normandie a beau être en France, quand on est installé en Savoie ça fait un peu loin pour une visite de courtoisie et surtout des livraisons régulières. L’entreprise cherche désormais à se fournir plus près, en Rhône-Alpes, ce qui lui permettrait d’allier au mieux commodité et réduction de son empreinte environnementale.
Créer l’alternative
A force de travailler le bambou et le lin, d’exploiter leurs propriétés et découvrir toujours plus de possibilités avec ces matériaux, une nouvelle idée émerge dans la tête de Félix : populariser les matériaux naturels et les faire connaître dans le monde de la mobilité douce comme de véritables alternatives aux métaux et à la fibre de carbone.
Pour concurrencer réellement le métal ou le carbone, une seule solution : l'industrialisation.
Pour y arriver, l’artisanat ne suffira pas et il faut franchir une étape cruciale : passer le cap de l’industrialisation, qui permettra d’augmenter les volumes et de réduire les prix. Mais si les processus industriels pour fabriquer un cadre de vélo en acier, en aluminium ou en carbone sont bien connus et documentés, il n’en est pas de même pour le bambou ou le lin…
Cyclik a donc passé deux années à expérimenter, notamment sur les liaisons en bio-composites de lin, avant d’en arriver au stade actuel. Dans ce bâtiment tout récent que la marque a investi en janvier 2023, elle travaille des pièces tournées en lamellé-collé de bambou (qui vient d’Espagne, faute d’industrie en France sur ce bois en particulier) et fabrique son propre composite à partir de différents tissus de fibre de lin, suivant la place prévue pour le « patch ».
Un composite de lin, c’est comme du carbone : on travaille avec ce qu’on appelle un « pré-imprégné », un tissu de fibre imprégné de résine qui assure la cohésion de l’ensemble. A l’heure actuelle, Cyclik utilise une résine bio à 56 % pour rester cohérente avec le reste de la démarche mais, dans l’absolu, cela fonctionnerait avec les mêmes résines que pour le carbone. Ensuite, selon la taille du fil et son tissage, on obtient des propriétés différentes.
Un vélo Cyclik issu du processus industriel compte 130 patchs de bio-composite de lin, aux différentes jonctions entre les tubes. Il y a ceux qui assurent la structure de la jonction et sa solidité, ceux qui sont là pour la finition…
Une fois les patchs préparés, ils sont assemblés dans un moule autour d’un noyau de cire et cuits pour leur donner leur forme finale, celle d’une jonction entre les tubes de bambou. On n’est pas surpris de voir Cyclik utiliser de la cire plutôt qu’une vessie : avec un point de fusion plus bas que celui de la résine, la cire peut être extraite facilement en chauffant la pièce à la sortie du moule, puis refondue en un nouveau noyau… dans la pièce d’à côté. Ici, on maîtrise le processus de A à Z !
D’ailleurs, si on a pu les visiter, vous ne verrez pas de photos des pièces dédiées à la mise en oeuvre de la cire et à la cuisson des jonctions en lin. Le processus développé par Cyclik est en instance de brevet et en attendant, la marque préfère garder le secret sur certains détails.
Côté bambou, c’est un peu plus simple : Cyclik reçoit des poutres de lamellé-collé en section carrée puis les fait tourner, voire évider pour certaines (pour le tube diagonal par exemple) chez deux fournisseurs, l’un en Isère et l’autre dans l’Ain. Du local, encore et toujours.
Ensuite, il n’y a plus qu’à passer à l’assemblage (par collage, tout simplement) puis aux dernières finitions. Félix nous indique qu’il faut compter 5 à 7 h de fabrication pour un cadre puis 2 à 3 h pour le montage d’un vélo, tous à assistance électrique pour l’instant. Entre le rouleau de lin – qu’on verrait plutôt dans un atelier de couture – et le vélo de ville qui roule sur le parking du bâtiment, il s’écoule donc une journée.
Avec l’effectif actuel – sept personnes depuis la conception des cadres ou la communication jusqu’à la fabrication et le montage -, Cyclik peut produire jusqu’à 500 cadres par an. Cependant, les capacités du lieu vont bien au-delà : l’atelier permet, en recrutant plus de monde, d’aller jusqu’à 1500 cadres par an. Alors qu’elle n’a même pas 10 ans, la marque se donne donc de quoi envisager l’avenir sereinement.
Le poids et la polyvalence comme arguments
L’avenir, chez Cyclik, c’est ça : un gravel à assistance électrique… ou non, présenté au dernier Roc d’Azur et qui arrivera pour de bon dans les premières semaines de 2025. A l’heure de notre passage, la marque était en train d’assembler un deuxième prototype – fonctionnel, cette fois – avec des jonctions usinées en aluminium pour les derniers tests avant la mise en production.
Le vélo est équipé du dernier système d’assistance Mahle XS, avec le moteur X20, qui permet d’offrir une plateforme « hybride » : comme le moteur est dans la roue arrière et la batterie sur le porte-bidon, on peut passer d’un vélo classique à un vélo à assistance électrique en un tour de main. Ou un changement de roue arrière, en l’occurence.
Dès le début de l’industrialisation, Cyclik s’est positionnée sur le segment des vélos à assistance électrique légère : ses vélos de villes sont équipés d’un moteur Mahle dans la roue arrière et une batterie discrète elle aussi (250 Wh), ce qui leur donne un bel avantage sur la balance en plus de simplifier le développement. La marque les annonce à 16,5 kg, soit 5 à 10 kg de moins que la plupart des vélos de ville à assistance électrique. Le gravel s’inscrit dans la même démarche, en poussant les choses encore plus loin.
Reste qu’on ne fait pas le même usage d’un vélo de ville que d’un gravel, et la conception de ce dernier n’a pas été de tout repos ainsi que nous l’explique Félix : « Le bambou filtre cinq fois plus les vibrations que le carbone et c’est plus ou moins la même chose pour le lin. Du coup, l’objectif c’est d’aller chercher de la rigidité car le matériau est très confortable intrinsèquement. » Cyclik ne s’interdit pas d’aller voir ailleurs pour trouver les propriétés qu’elle recherche, à une condition toutefois : « On n’est pas fixé sur le bambou et le lin, on explore d’autres pistes avec des matériaux naturels », complète Félix.
Le prix ? 4799 €, pour un poids autour de 13,9 kg. Si cela reste une belle somme, elle est comparable à d’autres gravel à assistance électrique conçus dans des matériaux plus conventionnels. Le premier pari de l’industrialisation est donc réussi mais il faudra maintenant convaincre sur le terrain. A ce sujet, un essai dans nos pages est d’ores et déjà prévu quand le vélo sera disponible. Rendez-vous dans quelques semaines !
Plus d’informations : cyclik.fr