Visite | Aivee : au coeur du moyeu
Par Paul Humbert -
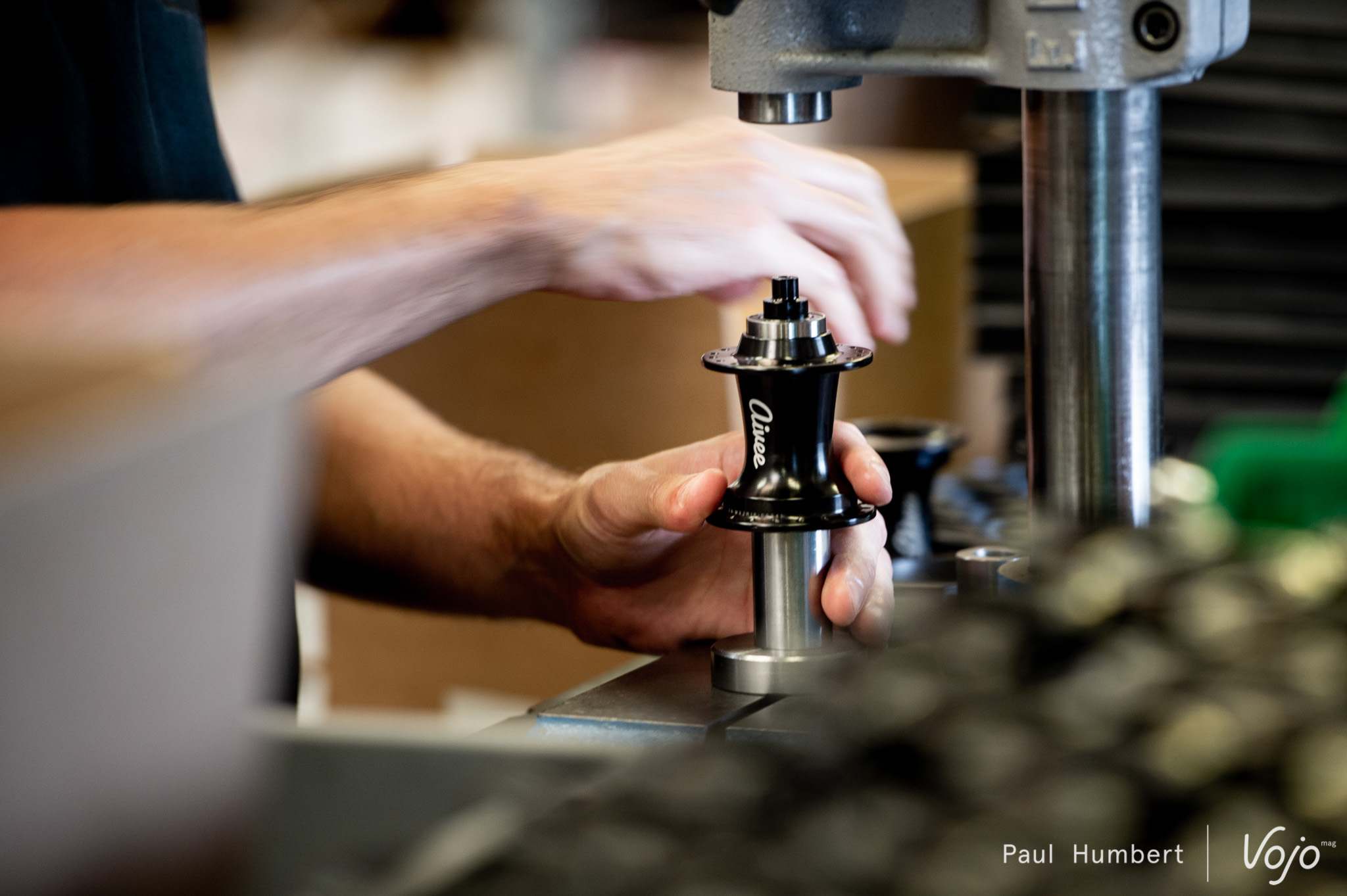
Il est assez rare qu’une entreprise de l’industrie du cycle élise domicile dans l’Ouest de la France. Elles sont pourtant quelques-unes, dont Aivee, à s’installer à quelques brasses de l’océan plutôt qu’à un coup de pédale des Alpes. Derrière Aivee, spécialiste du moyeu haut de gamme, se cachent de nombreuses associations, histoires et projets qu’on vous présente, les pieds dans un site de production « Made in France » :
Aivee, c’est également le petit bijou de Fidemeca-Bérieau, l’entreprise « mère » qui abrite le site de production des moyeux. Dédiée à l’usinage, le décolletage et l’assemblage de précision, l’entreprise est pilotée par Michel Bertrand et Jacques Clochard, des passionnés de vélo. L’activité « vélo » se mélange avec les pièces dédiées à l’aéronautique, l’aérospatiale, le ferroviaire ou encore celles dédiées aux activités médicales.
L’histoire serait trop simple si elle s’arrêtait là. Dans l’actionnariat, on retrouve Benoit Stupici et Nicolas Grossi qui sont également à la tête de l’entreprise Astérion, spécialisée dans le montage de roues. Aivee est donc piloté à quatre mains par des passionnés de vélos. Et pour en ajouter encore une petite couche, Fidemeca-Berieau a également des intérêts dans la société Astérion.
La synergie créée avec Astérion est loin d’être anodine puisqu’en plus de participer au développement des moyeux, le monteur utilise les produits dans l’assemblage des roues. Les deux marques sont bien distinctes mais intimement liées.
C’est d’ailleurs un des boss d’Astérion, Nicolas Grossi, qui sera notre guide chez Aivee. Sur place, nous rencontrerons Jacques Clochard, CEO aux commandes du groupe Fideip (auquel appartient « Fidemeca-Bérieau »), et Michel Bertrand, directeur général des sociétés Aivee et Fidemeca-Bérieau.
Sur place, à Sainte-Florence, dans la campagne vendéenne, on découvre un site de 6000 mètres carrés bourré de machine d’usinage, de décolletage et de postes d’assemblage. Dans le hall d’accueil de cette entreprise qui semble loin de toute activité « ludique », on repère de beaux moyeux et quelques paires de roues aux côtés d’échantillons des pièces produites sur place. On apprendra plus tard que les moyeux ont une place particulière chez Fidemeca-Bérieaux car ce sont les seuls produits finis produits sur place. Les autres partiront dans l’assemblage de trains, d’avions ou de satellites.
Derrière Aivee il y a, on vous le disait, plusieurs personnes, mais chez Fidemeca-bérieau, Michel Bertrand est l’homme clé du développement. Passionné de vélo depuis toujours, il a bricolé, conçu et développé à peu près tout ce qui pouvait s’installer sur un vélo : cadre, fourche suspendue, freins… Quand on parle de « bricolage », il nous reprend sur ce terme qu’il aime peu. Face aux réalisations, on réalise qu’un soin tout particulier est apporté à chaque produit et que tout est bien pensé. Il admettra tout de même ne pas avoir osé rouler avec toutes ses premières réalisations mais il a tout de même donné un coup de main à un certain Eric Baronne par le passé. À la tête d’un site grouillant de machines et de métaux en tous genres, il n’a pas fallu longtemps à Michel pour avoir envie de les utiliser pour concevoir ses pièces de VTT.
L’idée faisant son chemin, elle devient bien moins saugrenue et une opportunité « commerciale » se révèle aux yeux de l’entreprise une fois le précédent directeur de l’entreprise sur le départ. L’histoire commence avec une tige de selle puis des boitiers de pédaliers, rapidement jugés trop contraignants, et les moyeux s’imposent ensuite comme le produit à développer. L’ensemble des outils et des matières premières étant déjà sur place.
Naît alors Aivee, une petite « start-up » dans la grosse entreprise. Le capital « passion » est évidemment nécessaire mais il n’est rien sans le professionnalisme nécessaire à toute activité commerciale et industrielle. Le « grand » bénéficie du dynamisme et de la flexibilité du « petit » quand ce dernier peut se reposer sur son grand frère en cas de coup dur, comme ça a été le cas pendant une campagne de rappel.
Un moyeu est une pièce complexe et pleine de contraintes. Il doit s’adapter aux différentes tolérances, aux standards, aux pratiques et usages. Produire un moyeu haut de gamme « Made in France », ça ne s’improvise pas. Aux commandes du développement, on retrouve Benoit Stupici d’Astérion, en liaison directe avec Michel Bertrand pour la production. Il faut dire que le marché du cycle impose ses tendances et Astérion est aux premières loges pour entendre, s’adapter, développer et innover.
L’histoire d’Aivee est récente, et remonte à 2011 avec les premiers essais. D’abord orientés très « light », la philosophie des moyeux a changé et ils se veulent désormais plus polyvalents et ultra-fiables.
Le cheminement ne s’est pas fait sans quelques difficultés. Le premier moyeu « Edition One » de la marque était, de l’aveu de ses créateurs, plein de défauts. Les calages étaient anti-mécaniques et le tout manquait de fiabilité. Prenant conscience de tout cela, la marque a remplacé, et remplace toujours, le contenu de ces derniers. Le SAV est également la clé d’un service haut de gamme.
Concevoir un moyeu avec des monteurs, c’est aussi avoir l’assurance d’être bien en phase avec le produit fini que sera la roue de vélo. Pour arriver à tenir le niveau d’exigence que les fondateurs d’Aivee s’imposent, une année est nécessaire pour valider un produit. Ils passent tous à travers une large batterie de tests, et chez Fidemeca-Berieau, on sait comment tester des produits. Petite anecdote, l’entreprise fournit d’ailleurs Decathlon avec une machine développée pour tester des palmes !
Les tests s’effectuent avec des machines pour des mises en situation accélérées mais également avec des pilotes comme Pierre-Edouard Ferry ou Benoit Coulanges, même si l’équipe d’Aivee préfère finalement les retours de ses clients.
En entrant dans le coeur du site de production de Fidemeca-Berieau, Jacques Clochard, le directeur du groupe nous présente sa vision de l’activité. L’industrie en France peut être performante selon lui, elle a sa place dans la balance économique du pays et en investissant tous les ans, elle devient on ne peut plus légitime. C’est d’ailleurs encore plus valable dans une zone géographique qui n’est pas la plus dynamique. Serein, on nous ouvre les portes de ce qui est « tout sauf Zola ».
On en prend bien conscience dès l’entrée dans le site. Récent et bien organisé, il abrite de nombreuses machines et leurs régleurs-opérateurs. Au total, l’entreprise compte une centaine de salariés et collaborateurs. Dans l’atelier, pas de travail à la chaîne, les employés gèrent leurs machines, l’approvisionnement en matière première, le départ de l’outillage, les pré-réglages et tout le cycle de production.
Après avoir traversé les bureaux en franchissant la porte de l’atelier, on se retrouve devant un grand magasin qui abrite toutes les pièces d’outillage.
On passe ensuite devant les bacs de récupération des déchets solides et liquides qui sont triés par l’entreprise pour être recyclés. L’huile est séparée de l’eau, les déchets sont broyés et/ou revalorisés.
Dans les allées de l’atelier, on voit des stocks de pièces qu’il nous est difficile de reconnaitre, à l’exception des moyeux bien entendu. On passe donc devant des composants qui équiperont des enceintes de luxe, des axes en titane de pédales françaises bien connues, et des pièces pour les hélicoptères.
On déambule ensuite devant la zone de stockage des matériaux : aluminium, acier, titane, cuivre… On retrouve des barres de grandes et de petites sections, prêtes pour des opérations de décolletage ou d’usinage.
Les grandes barres de matière première sont positionnées à l’entrée des machines qui les « poussent » pour venir ensuite tailler dans la masse. Les opérations réalisables sont nombreuses et vous dire que nous avons tout en tête serait vous mentir.
Les pièces sont conçues dans différents matériaux selon un cahier des charges qui impose des contrôles et des tolérances restreintes. Des appareils de mesure et d’analyse complètent les rangées de machines et sur certaines séries, toutes les pièces sont passées dans plusieurs appareils de contrôle.
Les niveaux de contrôle et de précision vont jusqu’à 4, pour les pièces dédiées à une utilisation paramédicale, les moyeux sont classifiés en catégorie 3.
Tous les outils sont donc à disposition pour produire des moyeux. Après les premières étapes de production, les moyeux sont polis une fois jetés dans une machine remplie de coques de noix abrasives (et concassées).
Conçus, anodisés puis marqués, ils sont ensuite assemblés à l’étage de l’atelier. On retrouve deux monteurs au milieu d’un stock de pièces Aivee. La petite bulle « vélo » au coeur de la grosse machine. Sur les rayons, on retrouve donc toutes les pièces qui composeront le coeur de nos roues. On pourrait sourire en pensant qu’Aivee n’est qu’une simple distraction pour les passionnés de vélos à la tête de Fidemeca-Bérieau, mais Aivee compte maintenant parmi les 6 premiers « clients » de l’entreprise, et quand on voit avec quels produits ces petits moyeux sont en concurrence, on prend vite les choses plus au sérieux.
De l’atelier, les moyeux sont ensuite acheminés chez leurs clients ou chez les monteurs de roues comme Astérion et bien d’autres. C’est d’ailleurs là que la marque voit la plus grande perspective de développement. Il est vrai que « parler » d’un moyeu provoquera moins d’attente ou d’excitation aux yeux d’un public large que ce que peut susciter le lancement d’un nouveau vélo complet. C’est donc par la niche qu’Aivee entend bien s’imposer.
Devenir leader d’opinion, rester humble, et faire comprendre que la marque est fiable et là pour rester sont les objectifs d’Aivee. Avec une démarche haut de gamme, l’entreprise entend s’imposer chez les monteurs de roues pour équiper les plus belles paires de roues du marché.
Dans la même dynamique, l’entreprise s’est entourée d’un designer pour mettre au point un superbe banc de montage que nous découvrions à l’Eurobike. Un banc de montage que l’on aimerait avoir dans son salon, c’est bien une première.
Par cette niche, Aivee entend bien ensuite arriver dans le radar des grandes marques au moment d’équiper des vélos en série (en OEM). Aivee travaille déjà avec MFC, la Manufacture Française du Cycle voisine. Il faut dire que la production franco-française a du bon et la position géographique de l’entreprise permet une réactivité sans égal, surtout face à des concurrents asiatiques qui ajoutent des semaines de bateaux et d’arrêt en douane à chaque commande. Et on le sait, le temps, c’est de l’argent.
Apprendre de ses erreurs, proposer un produit pointu et fiable, s’appuyer sur des bases solides, voilà ce qu’Aivee met en place depuis plus de cinq ans. La maturité acquise, l’entreprise cherche maintenant la notoriété et on ne peut être qu’impressionné par la visite du coeur d’Aivee. De barres d’aluminiums à nos roues, il y a finalement beaucoup et peu de choses à la fois.
Plus d’infos sur le site de la marque : https://www.aivee.fr/fr/