Specialized Power Mirror & Fizik Antares Adaptative : la selle du futur sera imprimée !
Par Léo Kervran -
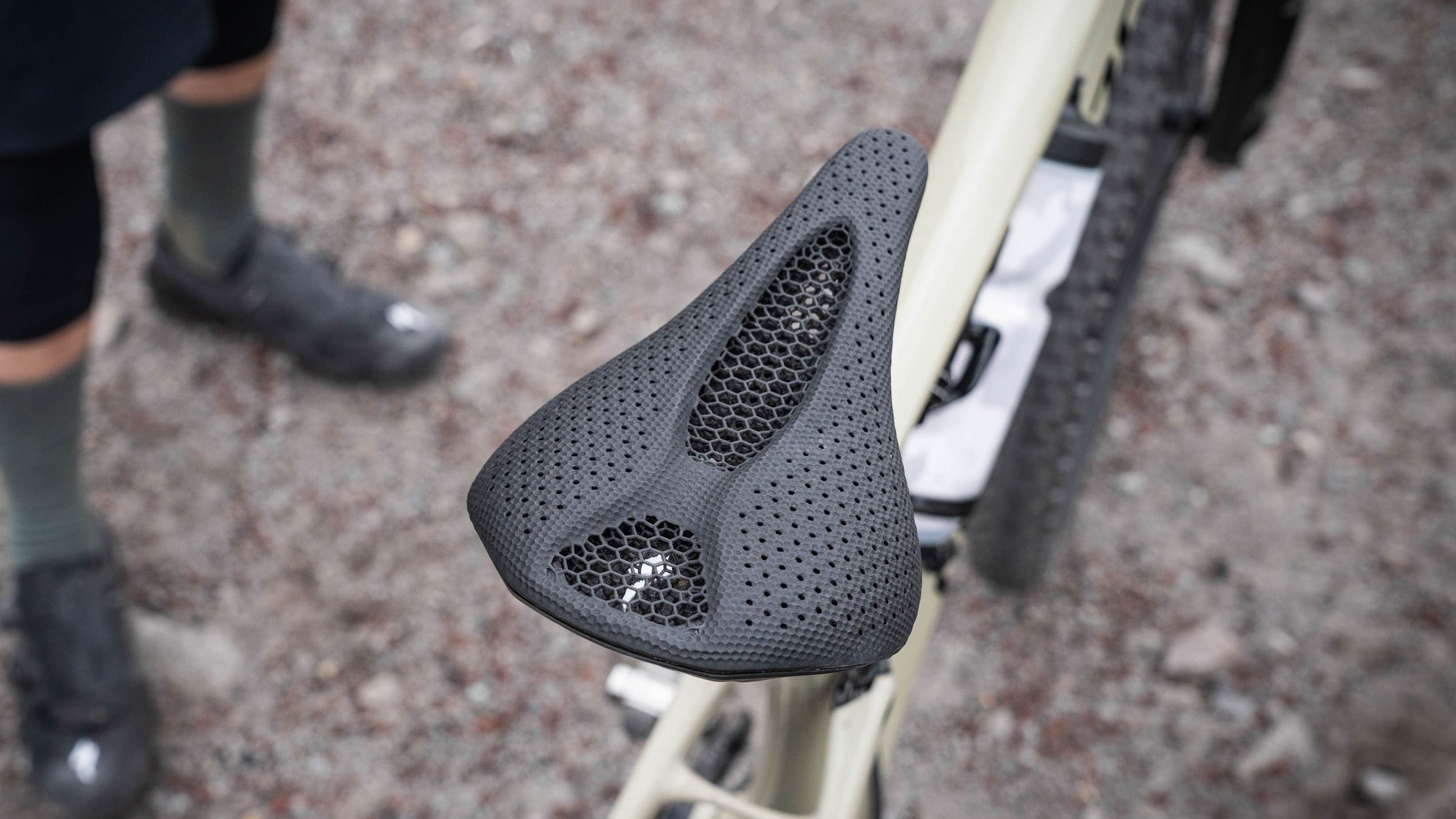
Specialized vient de présenter la Power Mirror, une nouvelle selle qui a la particularité d’avoir son rembourrage intégralement imprimé en 3D. Quelques mois après Fizik, c’est la deuxième marque d’envergure à se lancer dans l’aventure de l’impression 3D pour les selles. Quel est l’intérêt de cette technologie ? Ce procédé peut-il encore se développer pour nos composants ? Vojo s’est penché sur la question.
L’impression 3D, ce sont tous ces différents procédés qui permettent de fabriquer un objet en ajoutant ou en agglomérant de la matière (d’où le nom de fabrication additive), plutôt qu’en partant d’une base qui est ensuite creusée, coupée, taillée… La technologie a fait ses premiers pas dans les années 80, avec le premier brevet sur le sujet en 1984 et la première imprimante 3D en 1988, mais ce n’est que depuis 2010 environ que les choses se sont réellement accélérées.
Si les techniques et les matériaux diffèrent, le procédé de base est presque toujours le même : il consiste à « empiler » de très fines couches de matériau, jusqu’à former l’objet voulu. Aujourd’hui, on distingue 3 grandes familles de procédés de fabrication additive :
- La solidification d’une résine grâce à une lumière ou un laser : un laser se promène dans un « bain » de résine sensible à la lumière (ou photopolymère) pour former l’objet couche par couche. Lorsqu’une couche est terminée, le plateau descend dans le bain et le laser solidifie la couche suivante par-dessus.
- La solidification et l’agglomération d’une poudre grâce à un laser : même principe qu’avec une résine, le laser chauffe la poudre pour agglomérer et souder les grains entre eux. La plupart du temps, on utilise la technique du frittage, c’est-à-dire qu’on chauffe les grains sans les faire fondre, mais certains procédés fonctionnent par fusion.
- Le dépôt de fil fondu : l’imprimante chauffe un fil thermoplastique pour le déposer couche par couche sur une plaque de façon à former l’objet voulu. Une fois déposé, le fil refroidit rapidement et se solidifie, ce qui permet de déposer la couche suivante.
Fizik et Specialized font tous deux appel à la même technique, la solidification d’une résine grâce à un laser en structure type « nid d’abeille » à différentes densités suivant la place sur la selle. De la même façon, l’argumentaire pour justifier le choix de cette technologie est similaire chez les deux marques : elles estiment qu’elles sont arrivées aux limites de ce qu’il est possible de faire avec des mousses et la fabrication additive leur permet de bien mieux contrôler le rembourrage de leur selle pour les rendre plus confortables et plus durables sans faire grimper le poids.
La construction est également similaire avec une coque et des rails en carbone dans les deux cas, à la fois pour le poids et la déformation de la coque, quelque chose d’aussi important que le rembourrage lorsqu’on parle de confort d’assise. Seuls les dimensions et le poids diffèrent vraiment, puisque la Fizik est disponible en largeur de 139 mm (147 g) ou 146 mm (154 g) alors que la Specialized est un peu plus large : 143 mm (190 g) ou 155 mm (194 g). Côté prix, les deux modèles représentent le tout haut de gamme de leurs fabricants et comme toute innovation, le prix est (très) élevé : 390 € pour la Fizik et 399,90 € pour la Specialized.
Au-delà de ces deux selles révolutionnaires, ces nouveautés sont surtout le signe d’importants changements à venir dans la façon dont sont conçus nos vélos et nos composants. Jusque-là, l’impression 3D était l’apanage d’artisans ou de petites marques qui misaient sur la personnalisation pour de petits volumes. Que des grandes marques comme Fizik et surtout Specialized commencent à miser sur la fabrication additive montre que la technologie est prête et maîtrisée, ce qui signifie que son usage risque de progresser et de se développer rapidement. La question qui se pose désormais, c’est de savoir si d’ici quelques années, nous aurons tous des vélos et des composants parfaitement adaptés à nos caractéristiques personnelles.
Les deux fabricants ne comptent pour l’instant dans leur gamme que le modèle de série, en deux largeurs et sans aucune personnalisation, mais tous deux reconnaissent que l’étape suivante sera de proposer aux clients de personnaliser leur selle, en passant dans un magasin spécialement équipé par exemple.
Une équipe de scientifiques des universités du Wisconsin et de Caroline du Nord, aux Etats-Unis, s’est également penchée sur la question et a poussé jusqu’à chercher comment il serait possible de fabriquer une selle entière par fabrication additive. Leurs résultats, présentés lors la dernière conférence technique (virtuelle) de la Société des Ingénieurs Plasticiens en avril 2020, sont prometteurs.
Le procédé de départ est le même que celui utilisé par Fizik et Specialized : faire durcir une résine (ici à base d’epoxy) couche par couche jusqu’à lui faire prendre la forme d’une selle. Des adaptations sur la forme ont dû être faites pour l’impression 3D, comme une partie parfaitement plane à l’arrière de la selle pour faire le lien avec le support, mais de manière générale, le design de la selle n’a pas été beaucoup affecté.
Du fait des caractéristiques particulières de la résine utilisée pour l’étude, la selle devait être cuite après avoir été « imprimée ». Les auteurs en ont profité pour ajouter une bande de carbone en renfort sur toute la partie centrale, là où les pressions sont les plus importantes d’après leur simulation (vélo de route, mains sur les cocottes et en bas du cintre). Cette opération nécessite un peu plus de matériel que la précédente puisqu’il ne s’agit ni plus ni moins que de la cuisson d’une feuille de carbone avec de la résine. Il faut donc emballer la pièce dans un sac hermétique, faire le vide dans ce sac puis mettre l’ensemble dans un four adapté.
La limite n’est donc ni le temps ni la complexité mais bien le matériau.
Cette étude, réalisée avant tout pour montrer à l’industrie qu’il est possible de remplacer facilement le carbone sur certaines portions de selle sans affecter la production à grande échelle, montre aussi que nous ne sommes pas encore au point où chacun pourra se rendre dans un magasin pour prendre les mesures de son bassin et faire imprimer la selle parfaite. Néanmoins, on s’en rapproche de plus en plus : dans son ensemble, la fabrication de la selle a pris moins de 24h et son impression seule n’a durée « que » 11h. La limite n’est donc ni le temps ni la complexité mais bien le matériau. N’oublions pas qu’on parle ici de la coque d’une selle, pas de son rembourrage qui, si la coque est bien dessinée, peut être superflu. Lorsqu’on aura trouvé un matériau ou un procédé qui permettra d’imprimer une selle sans avoir à ensuite la passer dans un four, avec ou sans renfort en carbone, plus rien n’empêchera la personnalisation à volonté de nos composants.
On peut par exemple imaginer un fabricant de selle disposer d’une vingtaine ou une trentaine de formes de selle et/ou de rembourrages dans sa gamme mais seuls quelques-uns seraient produits pour la première monte, le reste étant disponible à l’état de fichier pour imprimante 3D. Une visite en magasin pour prendre ses mesures sur un système avec capteur de pression, comme Specialized le propose en partenariat avec Retül par exemple, et le magasin n’aurait plus qu’à imprimer en quelques heures la selle et/ou le rembourrage correspondant.
L’impression 3D est une technologie excitante par ce qu’elle permet en termes de développement et par le fait que certains procédés sont déjà accessibles à tous. En vélo, le domaine des selles est quelque chose de particulièrement sensible (sans jeu de mot) et s’il y a bien un composant qui a intérêt à être individualisé, c’est celui-ci. C’est donc une très bonne nouvelle qu’un fabricant généraliste comme Specialized se lance dans l’aventure après un spécialiste comme Fizik et on espère que cela va encore se développer. Quoi qu’il en soit, c’est un dossier à suivre de près !
Plus d’informations :
3D Printed Hybrid Composite Structures – Design and Optimization of a Bike Saddle